Key Performance Indicators (KPIs) are quantifiable metrics that measure critical success factors in businesses, department, or projects. When using CMMS software (Computerized Maintenance Management Software), tracking CMMS KPIs helps maintenance teams evaluate performance and identify areas for improvement. CMMS KPIs offer a clear way to monitor progress and optimize maintenance operations.
Why CMMS KPIs Are Important
Tracking KPIs is essential for any organization looking to improve maintenance management. Whether you run a small facility or a large manufacturing plant, KPIs provide valuable insights into performance. For example, CMMS KPIs can reveal areas where processes can be streamlined or where maintenance efforts can be redirected. In short, they help you track, measure, and refine your goals for better overall efficiency.
How to Set CMMS KPIs
Start by defining the organization’s mission, identifying stakeholders, and setting clear goals. KPIs are usually long-term metrics, but as goals evolve, so should your KPIs. Effective CMMS KPIs should be actionable and influenced by team efforts. It’s important that these KPIs are visible to employees and integrated into their daily tasks, as this fosters continuous reporting and improvement.
Common Types of CMMS KPIs
CMMS Key performance indicators generally fall into two categories: leading KPIs and lagging KPIs. Leading KPIs measure current performance, while lagging KPIs assess past performance. Both are critical for a well-rounded view of maintenance management.
- Leading KPIs:
- Number of Work Orders Completed Today
- Current Backlog Labor Hours
- Actual Cost vs. Budget Costs (Current)
- Lagging KPIs:
- Work Order Backlog Trend
- Mean Time to Repair (MTTR)
- Mean Time Between Failure (MTBF)
Key CMMS KPIs to Monitor
Mean Time to Repair (MTTR)
MTTR measures the average time required to repair a machine after failure. Calculated by dividing total downtime by the number of breakdowns, MTTR reveals how quickly equipment can be restored to operation. A lower MTTR indicates faster recovery times, helping maintenance teams improve responsiveness and efficiency. Monitoring this KPI ensures you’re continually improving your repair processes.
Mean Time Between Failure (MTBF)
MTBF tracks the average time between equipment failures. This KPI is essential for identifying problematic assets that require frequent repairs. Calculating MTBF is simple: divide total uptime by the number of breakdowns. Tracking MTBF helps identify which equipment needs more attention and preventive maintenance to extend its operational lifespan.
Visualizing CMMS KPIs with iMaint Dashboard
CMMS software like DPSI’s iMaint allows users to visualize KPIs in real-time through dashboards. For example, the MTTR and MTBF graphs refresh data automatically, helping managers monitor asset performance. Dashboards can display up to six KPIs simultaneously, giving you a comprehensive view of both leading and lagging indicators. These visual tools are vital for comparing current performance against organizational goals and adjusting maintenance strategies as needed.
Pictured Above: Mean Time Between Failure (MTBF) graph Component in iMaint Dashboard. This example was broken down by Craft (or the type of job such as mechanic, plumber, electrician) in order to determine which types of issues occur the most.
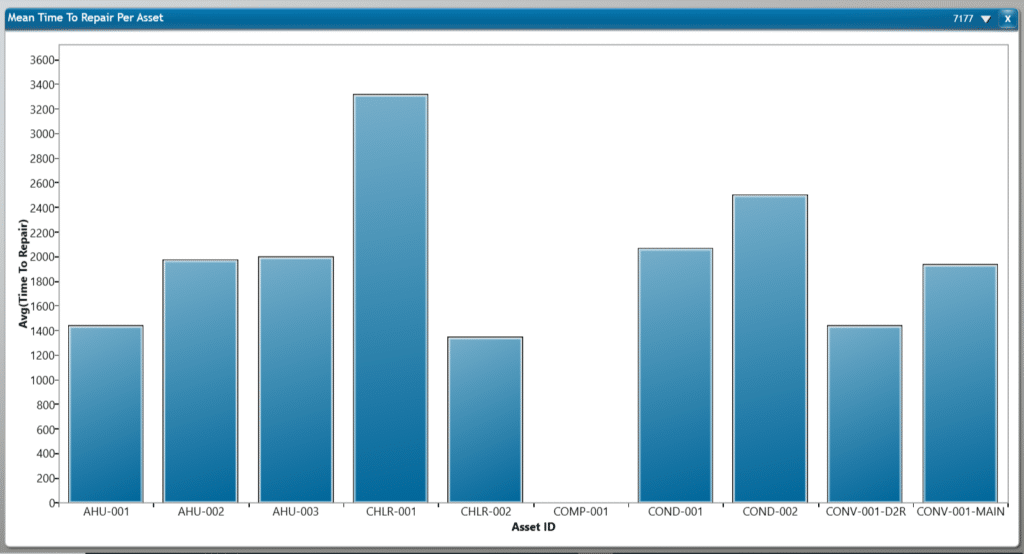
Conclusion: Why Every Organization Needs CMMS KPIs
Measuring CMMS KPIs helps companies continuously identify areas for improvement and promotes long-term growth. DPSI’s iMaint CMMS software offers a robust platform for tracking these KPIs, providing the data you need to optimize maintenance processes. To see how iMaint can streamline your operations, contact DPSI for a free demo today!